From farm to your doorstep: How is Kratom made?
FROM FARM TO YOUR DOORSTEP: HOW IS KRATOM MADE?
Growing and Harvesting
Nearly all of the kratom in the United States comes from Indonesia. Because of the warm tropical climate and rich soil, it creates the perfect environment to grow alkaloid-rich kratom. Plus, kratom has been used locally in the region for centuries, so farming techniques have already been put into place.
Humidity and lots of sunlight is imperative for this plant to thrive. This tropical evergreen tree can grow up to 100 feet tall, with vibrant green leaves that are harvested to create the product most know as kratom. The leaves are harvested at different points of maturity which could reflect different vein colors and alkaloid profiles depending on the time of harvest. Kratom vendors typically market vein colors as green, white and red.
The Drying Process
Once the leaves are harvested, the farmers will wash and clean the leaves of any debris. Then, they are put on racks to dry, either in direct sunlight or indoors under UV light depending on the farmer's technique. The color of the kratom can also depend on how long the leaves are dried.
Once the leaves are dried, industrial grinders are used to grind the kratom into a fine powder. Then, the powder is packaged into 1 kg or 25 kg bundles to be shipped off to United States’ ports.
Manufacturing Kratom
Once the packaged kratom reaches the Super Speciosa warehouse, carefully detailed steps are taken to ensure the product is safe and fully traceable from start to finish.
First, the shipment of kratom is inspected to make sure it has not been tampered with or damaged during shipping. Once the kratom shipment passes inspection, it is accounted for in inventory by assigning a lot number. This begins the traceability process.
The next step is the blending and batching process. The kratom goes through a blender that evenly mixes the product together, and then through a sifter to get any kind of dirt or debris out of the powder. The larger shipment is then broken down into smaller batches and assigned a batch number.

Hot spots of bacteria are common in herbal products. The blending process ensures that the samples sent to the third-party lab test is an accurate portrayal of that batch.
“For testing reasons, we want to mix the
Once the test results come back from the third-party lab, the Quality Control team goes through all the results and makes sure it meets the safety standards of the National Sanitation Foundation.
Once approved, the manufacturing team creates various products like stand-up pouch bags, kratom capsules, kratom teas and kratom tablets.

During the entire course of action, Good Manufacturing Practices (GMP) are followed and strictly enforced to provide safe kratom to Super Speciosa’s customers. The truth is, Indonesia’s kratom farmers don’t have a proper quality assurance process in place. One shipment could contain multiple different blends of kratom, or kratom that has been milled at different times. Super Speciosa’s quality control process has been proven to be safe and effective in order to produce the highest quality products possible.
“The people are the biggest components
Documentation is also a crucial part of GMP. Some of the many things that are documented are:
- Who received the product
- Who put the kratom through the batching and blending process
- Who sent out the samples to the lab
- Who allocated the batch
- How each machinery passed sanitation testing
- What date the rooms and machinery were cleaned
- How many units were yielded
- If there was any loss or shrinkage
Everything is recorded, and every person is held accountable, every step of the way. These documents are also routinely audited by the American Kratom Association and the FDA.
Ordering Kratom
Super Speciosa has implemented a seamless online ordering system to get kratom shipped out to the customer usually within 24 hours of ordering. The finished kratom product is transferred to the fulfillment warehouse, where packers are working around the clock to make sure the kratom is shipped out in a timely manner. As soon as the customer clicks “Place Order”, their order is sent directly to the fulfillment team and a label is printed. The order is then packed in discreet shipping boxes and picked up by USPS and UPS in the afternoon. The shipping process is so efficient, that all orders placed before 2 pm are shipped the same day.
The customer service department operates Monday through Friday, 9 am to 5 pm est. to handle any issues that may arise before, during or after the ordering process. Emails and phone calls, if missed, are returned within 24 hours. The team responds to all inquiries, and all customers are taken care of.
The systems Super Speciosa sets in place from start to finish, makes them one of the leading companies in the kratom industry.
“What separates us is our relationship. Other people in the industry might purchase their product from an unknown person. We have a great relationship with all our suppliers and growers,” states Barack.
Overall, Super Speciosa is always finding ways to make our process smooth and efficient.
“One of the biggest obstacles in production is that it’s always changing, it is dynamic,” adds Barack. “We have to change our processes, our records, to adapt to our technology, or the needs of the industry or consumer. To resolve it, we go through our records and processes and assess them. We communicate to our quality department and make the proper changes to our policy, procedures, processes, paperwork, anything that is going to make us adapt to that situation. We always want to improve everyday, whether it's increasing output in a given amount of time, better training, etc. We always are finding ways to be better to enhance our brand and to grow our people.”
Latest News

FDA Announces Intent to Add 7-Hydroxymitragynine to Schedule I

AHPA Policy Warns Against Labeling 7-Hydroxymitragynine as Kratom

FDA Targets 7-Hydroxymitragyine in String of Warning Letters to Producers

Rhode Island Becomes First State to Flip Kratom Ban
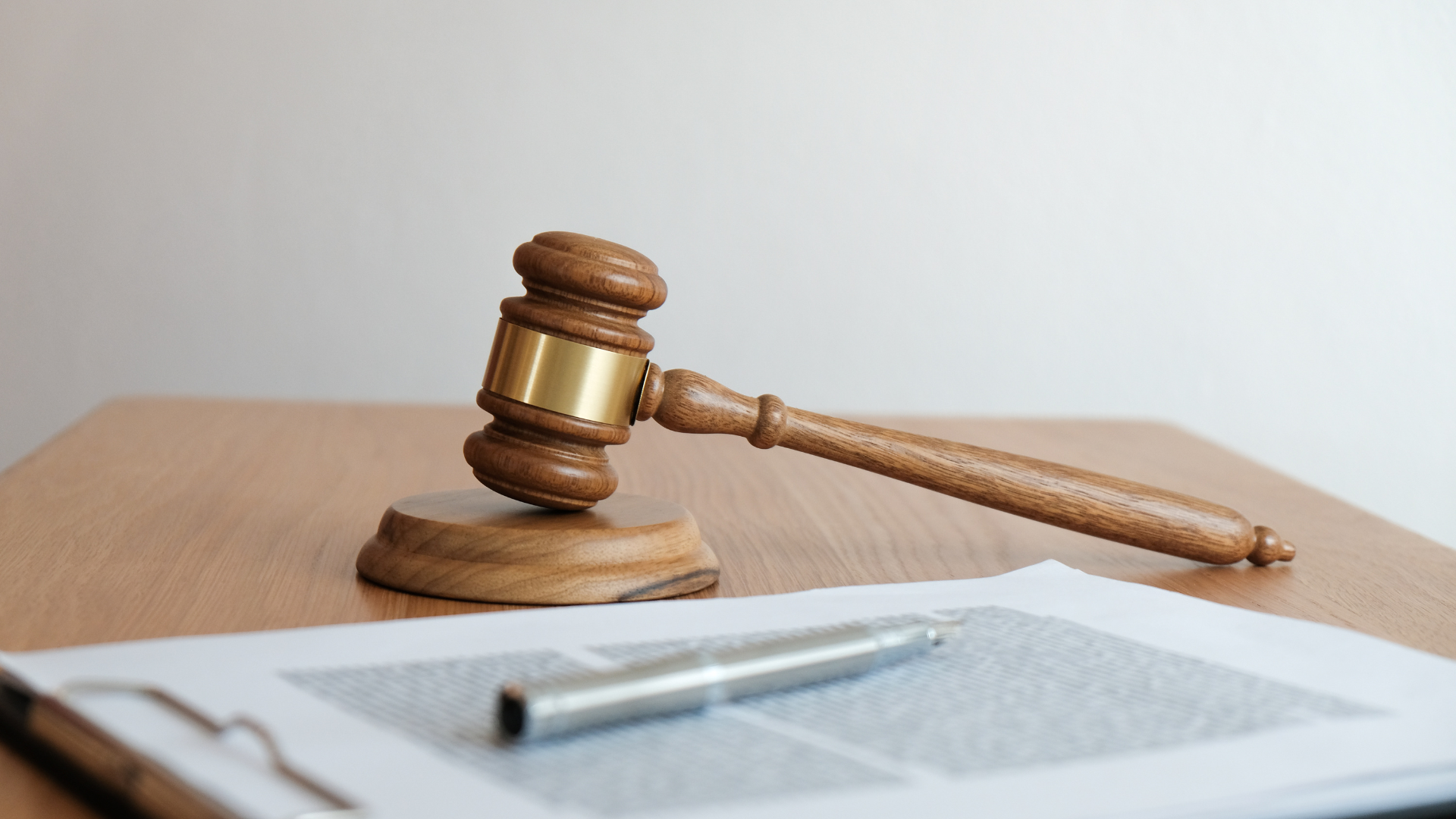
Louisiana Kratom Ban Enacted

Legislators Pass Kratom Ban in Connecticut

Legislative Update: Texas Squashes Ban Bill As Colorado and Mississippi Target 7-OH Products

Connecticut Lawmakers Pass Bill Scheduling Kratom as Part of Cannabis Reforms
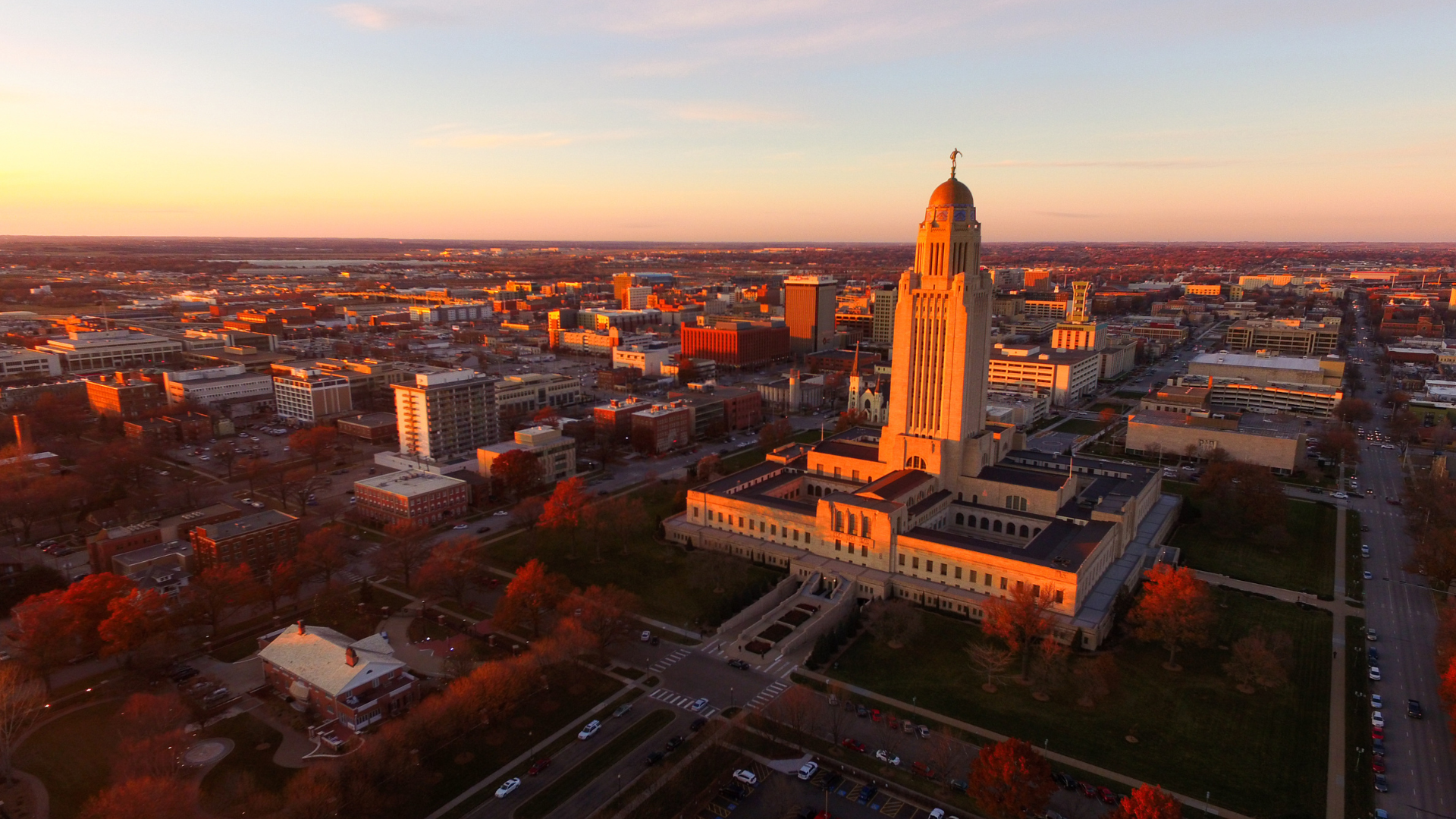
Nebraska Passes Kratom Consumer Protection Act, Shuts Down Proposed Ban

Indonesia Announces First Kratom Exports Under New Regulations
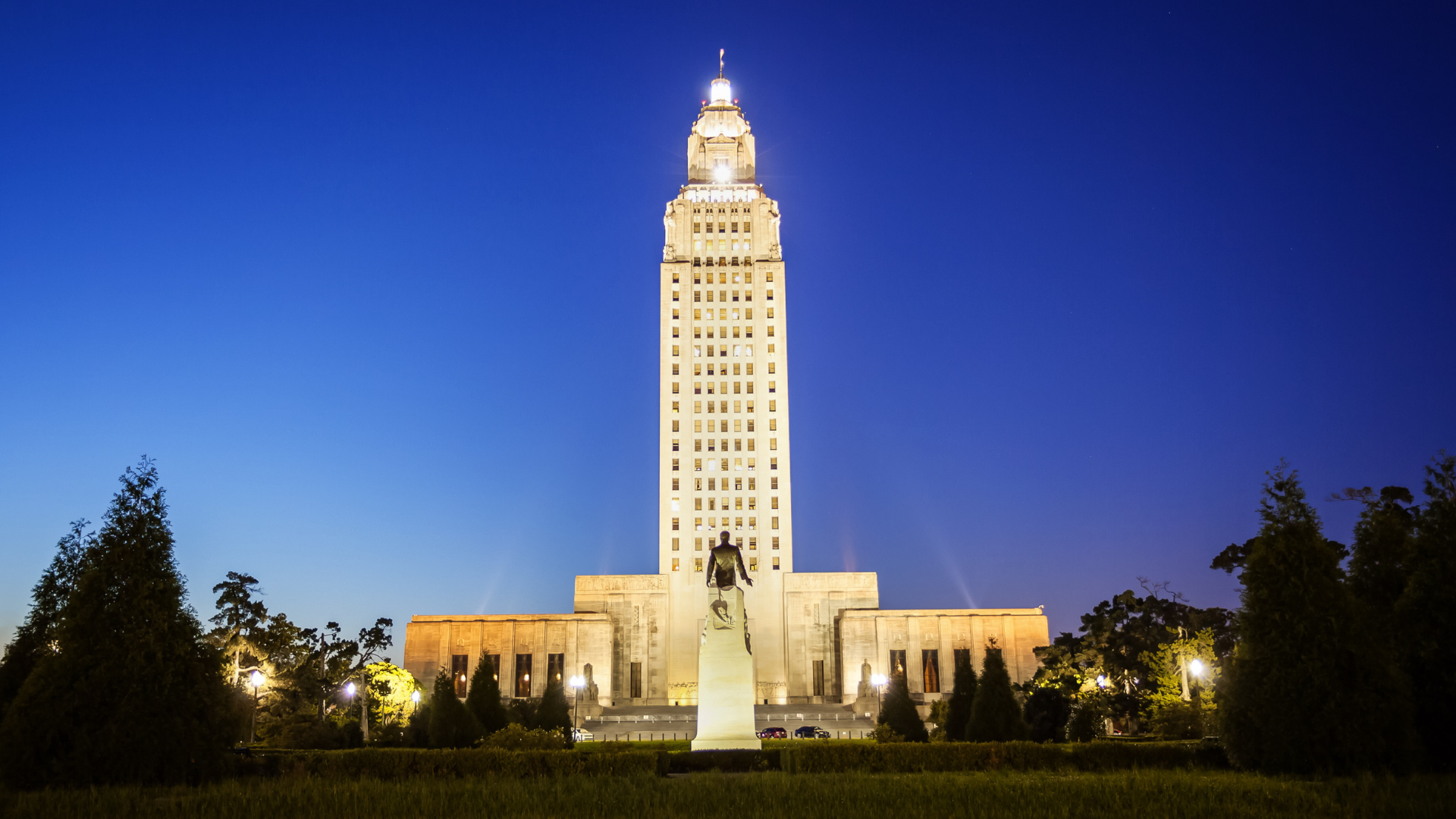
Louisiana One Step Away From Enacting Kratom Ban

South Carolina Lawmaker Reverses Course to Help State Pass Kratom Regulations
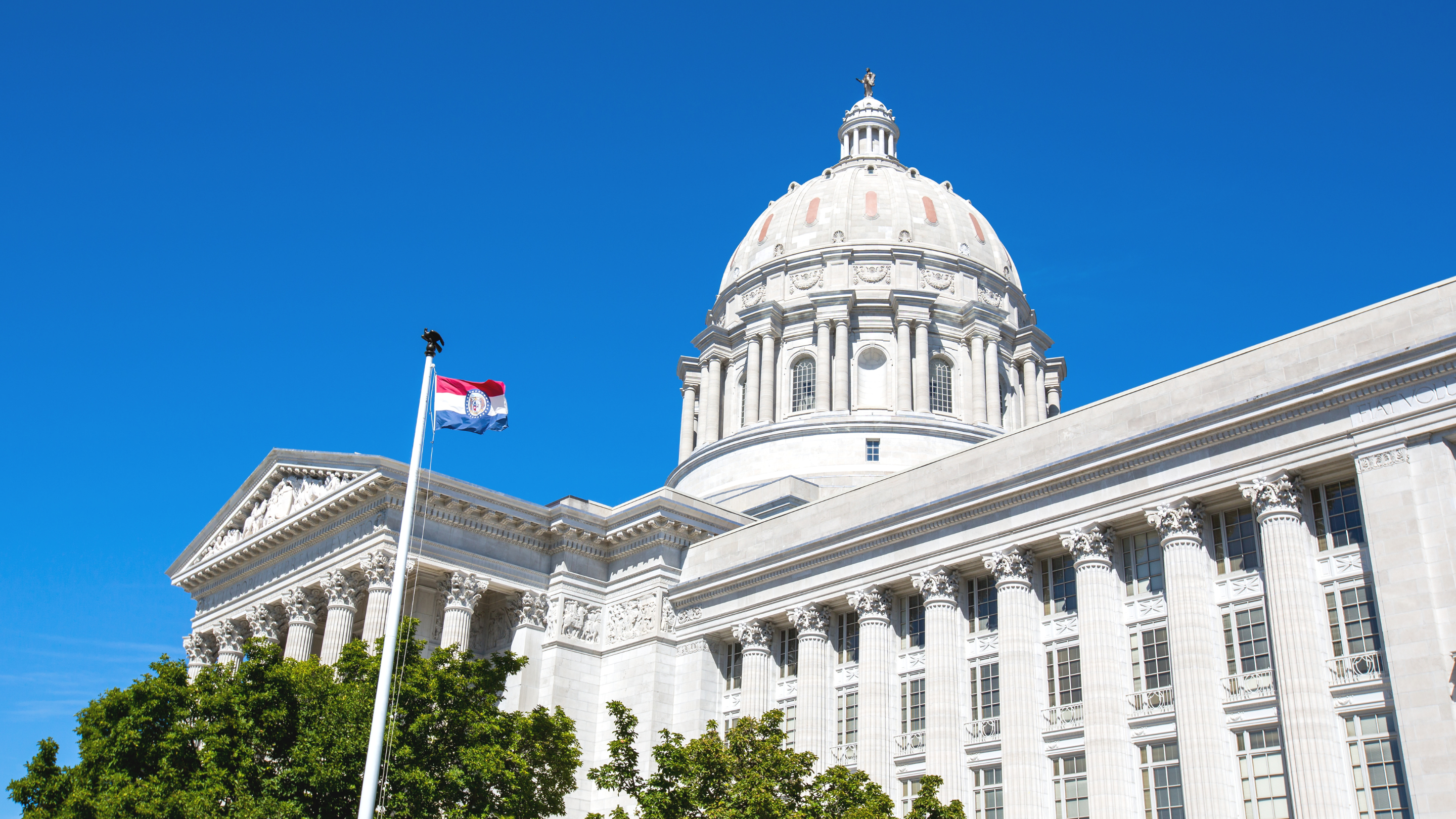
Missouri’s Fourth Attempt to Regulate Kratom Passes in House

Tennessee House of Representatives advances resolution opposing kratom, eyes ‘outright ban’
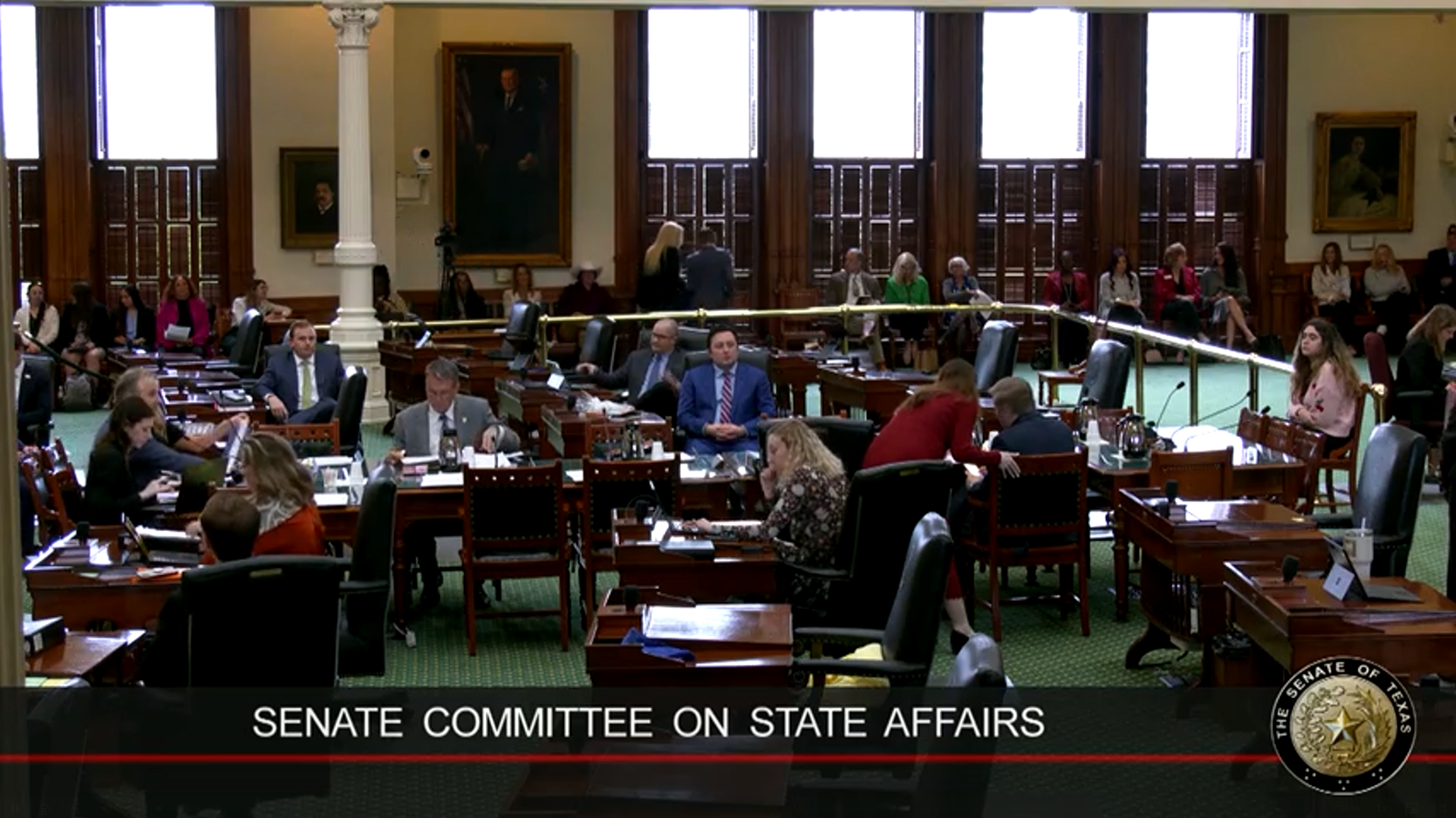
Lawmakers in Texas Consider Revisions, Restrictions to Existing KCPA